
Drag Racer (Scratch-Built)
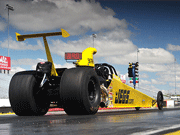
Scratch-built (or purpose-built) drag racers evolved from early production-based drag car developments. As production cars were stripped of all but the essential components for racing, there was recognition that the production car chassis had disadvantages for producing maximum acceleration, one of which was weight.
By using a scratch-built tube frame that removed the disadvantages, and enabled new advantages such as better weight distribution, the scratch-built drag racer was born.
Scratch-built drag racers are characterized by their unique chassis designs, slick tires and emphasis on maximum instantaneous straight line acceleration. No other type of race car is capable of generating as much acceleration and speed as the top scratch-built drag racers (Over 300 mph (480 km/h) in just a ¼ mile (0.4 km)). As the classes progress, bigger horsepower and bigger driving tires appear, alongside more safety and traction aids.
Scratch-built drag racers are built in two configurations: Front engine-Rear Drive and Mid-Engine-Rear Drive. Two styles predominate: Those with a body shell that appears like a production car, and dragsters which are long, slender single seat machines.
Racing is held on local drag strips in almost every part of the world.
Drag Racer (Scratch-Built) Contents
Power and Weight Stats | |
Horsepower (Typical Range) | 500-1200 |
Race Weight (Typical Range) | 998-1135 kg 2200-2500 lb |
Design and Construction
Race Car Models/Classes of This Type
Dragster, Funny Car, Top Dragster, Super Comp, Comp, Top Alcohol Funny Car, Top Alcohol Dragster, Pro Stock, Top Fuel
Build Your Own Scratch-Built Drag Racer
Knowledge Level
To build a drag racer from scratch requires design knowledge in handling, chassis, suspension, powertrain, aerodynamic and safety. Handling, suspension and powertrain are especially important as both areas directly affect how the power is generated, how it is transferred to the tires, and how the car's weight distribution is used to generate traction and acceleration.
Design Challenges
Weight Distribution: Weight transfer to the driving tires upon launch is critical in drag racing. The greater the weight transferred the better to increase grip and reduce wheel spin. As the front of the car is frequently lifted off the ground, care must be taken to ensure even Left/Right weight distribution and that the suspension and tires are setup as closely as possible to give a straight launch.
Suspension: Suspension, within the rules should permit maximum weight transfer to the driving tires and remain compliant to the road surface. On rear drive vehicles, it is important to ensure the geometry of the rear suspension has the correct amount of anti-squat. The force vector that originates from the tire contact patch, through the instant center of the suspension and into the chassis determines a great deal about how weight is transferred to the rear tires throughout the run. Consequently, you should design rear suspension geometry carefully, and match springs and shocks for the expected forces.
Where no suspension is used, the chassis can be designed to provide additional flex that enables weight to be transferred.
Chassis: The driver safety cell, engine/driveline/aero component mounts and chassis flexibility are key considerations. Packaging of components for optimal weight distribution within the chassis.
Powertrain: Depending on the drive configuration and class regulations, there are modifications that can be made to the powertrain to increase power, maximize its delivery to the tires, and optimize weight distribution.
Increasing power: Forced induction (Super/turbochargers), freer flowing intake/exhaust, fuels
Gearing: Gearing for the engines power band will use the power the engine produces in the most efficient way.
Limited slip differentials: Putting power down to both wheels to aid traction
Drivetrain weight distribution: Moving heavy items like batteries toward the rear of a rear wheel drive vehicle will aid traction.
Aerodynamic: In classes where aerodynamic modifications can be made (i.e. Wings/spoilers added for traction purposes, body drag reduction), there may be merit to making these changes. Reducing drag during acceleration is always a good thing. In the case of wings/spoilers, the speeds required to produce sufficient downforce and the drag generated by the aero devices must be evaluated to ensure there is a real increase in performance over the loss in acceleration from wheel spin.
Safety: A crash/rollover safety cell for the driver must be integrated into the chassis design along with a racing seat/harness. Padding on the roll-cage can be used to prevent injury. Consideration should also be given to fuel safety cells and fire protection (firewall)
If you intend to race under a sanctioning body, always read and understand the regulations of your chosen racing class before designing or building any race vehicle.
Design Resources
Learn the basics about race cars and race car design from our free online knowledge series
Download our free race car design aids to assist you designing your race vehicle.
In-depth books and learning resources we recommend for scratch-built drag racer design.
Join our forum to ask and find answers to your scratch-built drag racer design/construction questions.
Construction Challenges
Due to the precision that is associated with the tuning and performance of scratch-built drag race cars, ensuring the chassis is dimensionally accurate and straight is key. The use of a solid, flat and level build space is important. Jigs are often used in this case to ensure that structural tubing stays in alignment during welding/brazing.
The builder should have solid joining and metal working knowledge and skills when fabricating the chassis/rollcage/suspension. While mild steel (1018/1020) is very forgiving, some metals are best welded using a specific method (mig/tig) and some require heat treatments before and following welding to restore their toughness and strength.
Having sufficient space for the chassis and bodywork construction is important, as a cramped workshop can be difficult to work in.
The tools to fabricate the chassis and bodywork can add considerably to the cost of your project if you don't already have a workshop, but borrowing or renting items is also an option.
Many customized components can be farmed out to speed shops or fabrication shops, but if you are interested in learning the skills yourself, the same money can be spent on equipment and teaching yourself.
Build Costs
Build costs for more entry-level scratch-built cars can be similar with purchasing and modifying a production-based vehicle. The biggest difference is in build effort (see below), which if built using your own labour won't add to the cost.
As the engine power output increases so do the costs for engine, driveline and other components. Most entry-mid level engines are built on production blocks and their costs are still relatively acceptable to the amateur racer. However, with increasing power there is a point where costs rise rapidly due to the materials, engineering and fabrication required to produce parts that can withstand the stresses.
Build Effort
Because the car is scratch-built, there will be significant effort in design and construction. There is however, an equally great satisfaction and sense of accomplishment at being one of the few people in the world who have built their own race car from the ground up!
Racing Cost
Tires, engine and drivetrain components probably form the single largest expense. As power and speeds rise, tire costs, engine rebuilds and driveline rebuilds tend to become more frequent. Depending on your mechanical skills or willingness to learn, the costs of rebuilding the engine and driveline can be limited to parts if you do it yourself.
Transportation and Support Equipment
Trailering required.
