
Car Chassis Basics and How-To Design Tips cont…
Which Chassis Type to Choose?
The complexity of designing and building the chassis and the ambiguity in detecting damaging in a monocoque leads most amateur designers to stick with the spaceframe chassis—easier to design, build and operate. The tools and learning curve are far easier to manage as well.
Yet, if you are interested in the monocoque chassis, do go out and learn as much as you can and experiment with the techniques of design and fabrication.
If a career in engineering is your goal, then knowledge of both spaceframe design and monocoque design will serve you well in many fields.
Modeling a Chassis
Before building your vehicle, consider building models to aid in visualizing design. Some may prefer to stick with computer tools like FEA (Finite Element Analysis) software, but for sheer hands-on visualization, we recommend building your own balsa spaceframe models or using paper or crafts materials to form a monocoque.
As the photo MOD1 below from Herb Adam’s book Chassis Engineering shows, these models can provide insight into the design and torsional rigidity of various configurations:
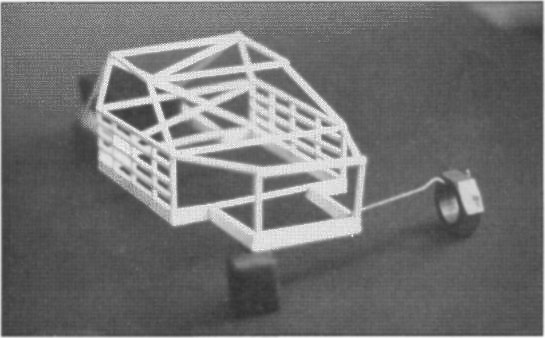
Diagram MOD1. Balsa model of a chassis shown in Herb Adam’s book “Chassis Engineering: Chassis Design, Building & Tuning for High Performance Handling”
Chassis Structural Materials/Shapes
Designing a chassis, be it spaceframe or monocoque requires an understanding of the right materials and their engineering properties. We’ll take a look at some of the basic materials used, but there are whole books available which cover the topic in the detail that a scratch-builder will need.
Structural Materials
Most modern spaceframes are built using steel structural tubing in grades 1018, 1020 or 4130 chromoly. The first two grades are considered mild steel with sufficient strength and toughness for amateur car builders. These grades are not affected by welding heat and do not require post-welding heat treatment. The 4130 chromoly grade, while stronger than mild steel, does require post-welding heat treatment to restore its mechanical properties.
Steel is very good from a metal fatigue perspective and due to the vibration and oscillating loads encountered in cars and trucks, it is the preferred material for amateur builders who’s goals are long chassis life and dependable strength.
Aluminum has been used in spaceframe design and can provide weight savings but depending on the grade, it may or may not be weldable. The fatigue life and strength should be understood before selecting aluminum as your spaceframe material.
For monocoque builders, the materials most often used today is fiber reinforced plastic (FRP). The fiber can be anything from fiberglass to carbon fiber, depending on the requirement to save weight. The plastic is generally 2-part epoxy. Builders make use of composite sandwich structures by laminating FRP over a honeycomb structure. These “Panels” are very rigid in bending. Forbes Airde, in his book “Race Car Chassis Design and Construction” provides a chart (Diagram SM1 below) showing how composite sandwiches, while almost 4 times as thick as steel weigh only 1/5th the weight of steel for the same bending strength.
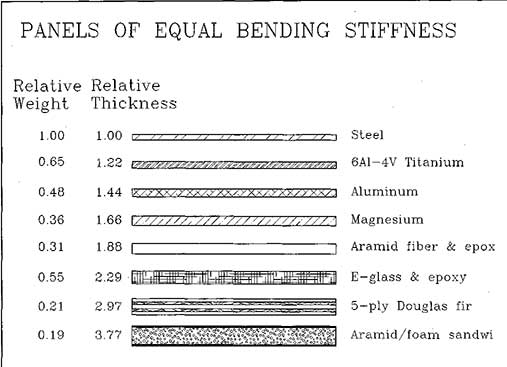
Diagram SM1. Chart from Forbes Airde’s book “The Race Car Chassis : Design, Structures and Materials for Road, Drag and Circle Track Open- and Closed-Wheel Chassis ”. While thicker than steel, panels made of other materials can provide equivalent strength while weighing less.
Structural Shapes
The selection of structural shapes for spaceframe construction provides the designer with flexibility in how they optimize their chassis designs. In diagram SS1 below, the most popular shapes are shown:
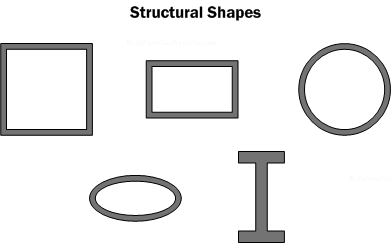
Diagram SS1. Structural shapes
Square and rectangular tubing provides the easiest design and fabrication. As mentioned earlier, cutting and welding/brazing is the easiest with square or rectangular shapes. Rectangular tubing also provides the opportunity to create a “Beam-like” structure where more strength is required on one axis than the other. Square and rectangular 4130 chromoly is also available, but generally at a higher cost than circular.
Circular tubing, while not as easy to fabricate with, is widely available in 4130 chromoly, so to take advantage of the increased strength or reduced weight for the same strength, circular (and oval) may be the shape of choice.
Oval tubing is popular for use in exposed wishbones on open-wheel type race cars. Its shape is more aerodynamic than round or square tubing and therefore it creates less drag and turbulence. The downside is that it is not as structurally strong as round or square tubing in bending (Along the narrower dimension).
The I-Beam type shape may be useful where deflection (bending) along the “I” vertical axis needs to be minimized over a span. In long span situations, square tubing will not fare as well as I-beam in terms of deflection.
Chassis Design Tips (2/2)
Layout the tube members for easy access and maintenance
Maintaining a car comes after construction. Placing tubes across openings is a natural way of ensuring a rigid chassis. However, in practical terms you may be making it difficult or impossible to reach the maintenance demanding components. A good chassis design will allow quick and easy access to all components and will not hamper removal or replacement of any part.
Check out vehicles which are competitive in your class
Vehicles which are competitive are usually built well, and with appropriate materials and methods. Observe them at the track and in the pits, and you can infer a great deal about what makes them winners.
Optimize the tubing shape for the job
Square tubing is the easiest structural shape to build a chassis from. However, there are circumstances where round tubing can be useful, albeit at a penalty in the complexity of construction. Oval tubing is useful in open wheel race cars for wishbones.
Optimize the tubing size and gauge for the job
Tubing which is used in tension, can be of a lighter gauge than that used in compression. Keeping this in mind can save considerable weight, although it requires additional joining work and variety of tubing.
Choose the right material
Many road and race car chassis are built using mild steel in the 1018 or 1020 grade (anything lower than 1018 is not advisable due to its limited strength). There is nothing wrong with using these grades if the chassis is properly designed and weight is not the utmost concern. 1018 and 1020 don’t require heat treatment after welding and can be MIG welded, making fabrication easier.
If weight is a concern, then many builders opt for 4130 Chromoly. The same strength can be had with 4130 for less weight than mild steel. However, depending on how you join your tubing, you may need to heat treat the finished product. 4130 also usually comes in round, which is more difficult to fabricate but aircraft builder suppliers can provide square 4130 at a higher price.
The key point to consider is the need for weight saving. If weight is not a concern, you may wish to opt for the easier to fabricate mild steel. If it is, then you may have limited choices outside of 4130.
Recommended Further Reading
Chassis Engineering: Chassis Design, Building & Tuning for High Performance Handling Chassis Engineering is a great introduction to race car design. In a practical and down-to-earth way, it covers the fundamentals of how race cars handle and the requirements for designing and constructing a car. The book includes chapters on chassis design, suspension design, frame construction, aerodynamics and tuning. Overall it provides the reader with the foundation of how the key components of a race car work and interact together.
Get "Chassis Engineering: Chassis Design, Building & Tuning for High Performance Handling":The Race Car Chassis : Design, Structures and Materials for Road, Drag and Circle Track Open- and Closed-Wheel Chassis Covers the history, different types, structures and materials of race car chassis. It also delves into the various types of suspensions. This book is not a detailed design book, but does provide good information and plenty of different race car examples for those seeking to understand chassis design.
Get "The Race Car Chassis : Design, Structures and Materials for Road, Drag and Circle Track Open- and Closed-Wheel Chassis":- View all chassis books
Continue on to Car Powertrain Basics and Tips…
44 1 24 2
